Relative Properties Of Magicut Grades |
Correct Grinding |
|
|
Depending on the nature of cutting operation like ease of cutting, hardness of job, machinability of the job, speed of cutting and heat generated at the cutting action the right grade of tool is to be selected. The relative hot hardness, wear resistance and toughness of various grades are indicated in the chart |
|
|
The heat generated while grinding the cutting edges reduces the hardness at the cutting edges, thereby lowering the cutting efficiency of a sharpened tool. Therefore, when grinding tool bits: |
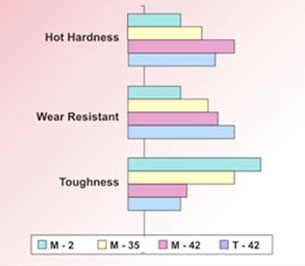 |
- Use a soft wheel, appropriately dressed.
- Apply light pressure and constantly rotate the tool bit surface to avoid discolouration or burning of the cutting edge.
- Avoid sudden change of temperature DO NOT dip the hot tool in cold water (otherwise the tool will develop surface cracks, which reduce the tool efficiency and life).
- Hand stoning of the finish ground faces lengthens life between regrinds and enhances surface finish achieved with finishing cuts.
Correct Form
To get high cutting efficiency it is vital that correct tool geometry (profile) is maintained when regrinding the tool. Correct grinding of various angles of a tool can greatly improve the tool bit's performance. Please refer to the chart for details of correct angles for cutting different materials. |
|
|
Recommended Tool Geometry |
|
|
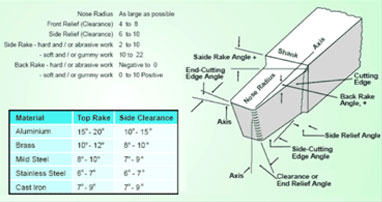 |
|
|
|
|
|
Tool Bits should be fitted in the tool post or tool holder with a minimum of overhang as shown below (in the ratio of 1:1 of the tool size or less). The base of the tool bit should be flush with the tool post. When shims are used they should |
|
cover the entire length of the tool bit that rests on the tool post.It is not advisable to use a bent shim.
Tool bits can break at section XX as shown in figures 1, 2 & 3 |
|